CASE STUDY
Chiller Plant Upgrade
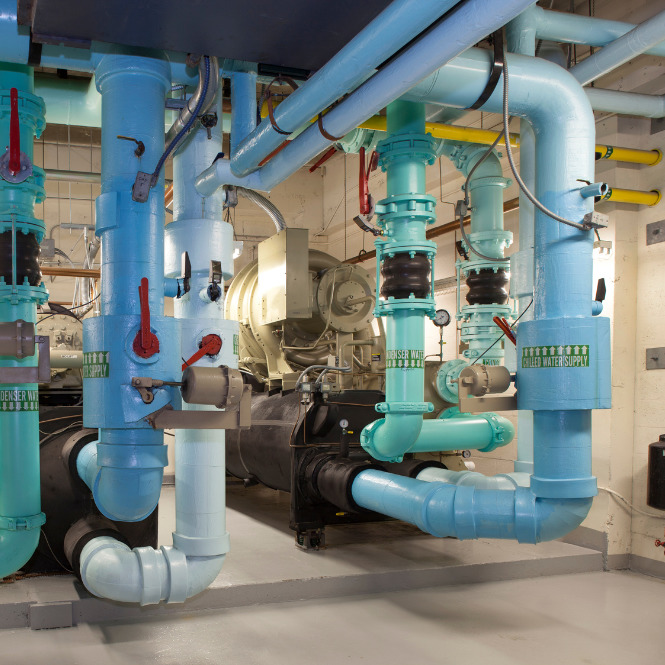
Project Overview
High temperature alarms and automatic shut-downs were plaguing a new aerospace coating process. The resulting production interruptions were having a significant impact on profitability. IPD was contracted to troubleshoot the new coating process cooling system with the goal of “zero capacity loss and downtime reductions.” A site audit and process evaluation determined a replacement with a larger chiller, supplemented with a trim chiller to satisfy peak demand, would satisfy both objectives.
The project began with energy, process and hydraulic studies to properly define the solution and specify equipment. A new mechanical building and integration of the chillers, cooling water pumps, buffer tank and associated piping required close collaboration with the Client. In addition, electrical instrumentation and controls, concrete foundations, and structural pipe racks were part of the scope. Provisions for a future auxiliary chiller and system expansion were incorporated into the design.
CHALLENGE
Integration of new equipment into an existing manufacturing facility is always a challenge. Trying to place equipment into a crowded space requires experience, creativity, attention to detail.
SOLUTION
Working closely with client personnel, IPD reviewed design concepts with all stakeholders to ensure installation was possible and that interference and issues were addressed early in the design phase. Operator access was a top priority. The final design provided sufficient clearance so that maintenance could be performed quickly and downtime minimized.
RESULT
The Client received a properly sized, efficient, reliable, and maintainable chilled water system, with spare capacity for future plant expansion. All operational objectives were achieved and the facility is currently recognizing the performance benefits of the new system.
More case studies
Click to view more examples of IPD's work: